
Position Sensing Solutions
Position sensors are widely used in closed-loop mechanical control systems across a wide variety of industries including automotive, industrial automation, process control, and military and aerospace. Analog Devices provides signal chain solutions for most common, high-precision position sensors such as optical encoders, resolvers, and LVDTs and magnetic sensors (AMR, TMR, Hall). Our signal chain solutions ensure that position measurement is done accurately, optimizing overall solution size and power consumption.
Value and Benefits
Our broad portfolio of solutions provide accurate position sensing required to enable mechanical systems to precisely and intelligently perform tasks across a variety of applications. Optimized for overall size and power consumption, our solutions offer signal chain and reference designs that accelerate your position sensing designs and are ideal for common high-precision sensor types, including optical encoders, resolvers, LVDTs, and magnetic sensors.
Offers signal chain and reference design solutions to accelerate your position sensing designs
Includes solutions for common high precision sensor types
Optimizes solution size and power consumption

Solution Resources
Optical Encoder
Interactive Signal Chains
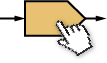

Training and Support
Trainings and Tutorials
Files and Downloads
{{modalTitle}}
{{modalDescription}}
{{dropdownTitle}}
- {{defaultSelectedText}} {{#each projectNames}}
- {{name}} {{/each}} {{#if newProjectText}}
-
{{newProjectText}}
{{/if}}
{{newProjectTitle}}
{{projectNameErrorText}}