Low Power Boost Regulator with Dual Half-Bridge in 3mm × 2mm DFN Drives MEMS and Piezo Actuators
Low Power Boost Regulator with Dual Half-Bridge in 3mm × 2mm DFN Drives MEMS and Piezo Actuators
2009年09月01日
Introduction
Advances in manufacturing technology have made it possible for actuators, sensors, RF relays, and other moveable parts to be manufactured at a very small scale. These devices, referred to as MEMS (micro-electro-mechanical systems) or micro-machines, are finding their way into daily life in applications unheard of just a few years ago. MEMS are used in automotive, military, medical and consumer product applications.
Many types of MEMS devices consume very little power to operate and generally require the use of two support circuits, a step-up converter and a dual half-bridge driver. These support circuits must be very small and highly efficient to keep pace with ever-shrinking MEMS applications. To this end, the LT8415 integrates the step-up converter power switch and diode and the dual half-bridge driver in a 12-pin, 3mm × 2mm DFN package. Its novel switching architecture consumes very little power throughout the load range, making it an ideal match for driving low current MEMS.
The LT8415 generates output voltages up to 40V from sources ranging from 2.5V to 16V. The output is then available for the integrated complementary half-bridge drivers and is available via OUT1 and OUT2 (see Figure 1). Each half-bridge is made up of an N-channel MOSFET and a P-channel MOSFET, which are synchronously controlled by a single pin and never turn on at the same time. OUT1 and OUT2 are of the same polarity as IN1 and IN2, respectively. When the part is turned off, all MOSFETs are turned off, and the OUT1 and OUT2 nodes revert to a high impedance state with 20MΩ pull-down resistors to ground.
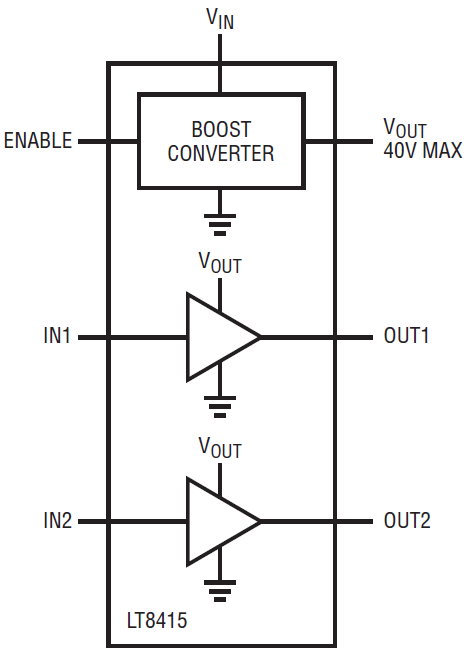
Figure 1. Simplified block diagram of the LT8415.
2.6V–5V Input to 34V Output MEMS Driver
Figure 2 shows a MEMS driver that takes a 2.6V–5V input and produces a 34V output. This circuit draws very little source current when the dual half-bridge is disabled. The input current is only 320µA at 2.6VIN and 128µA at 5VIN. A logic level signal at IN1 and IN2 activates the dual half-bridge switches. Figure 3 shows the turn-on delay and rise time for OUT1 and OUT2 with both half-bridges activated. Figure 4 shows the turn-off delay and fall time with the 200pF and 1nF capacitive loads shown in Figure 2. See the data sheet details for measuring delay time.
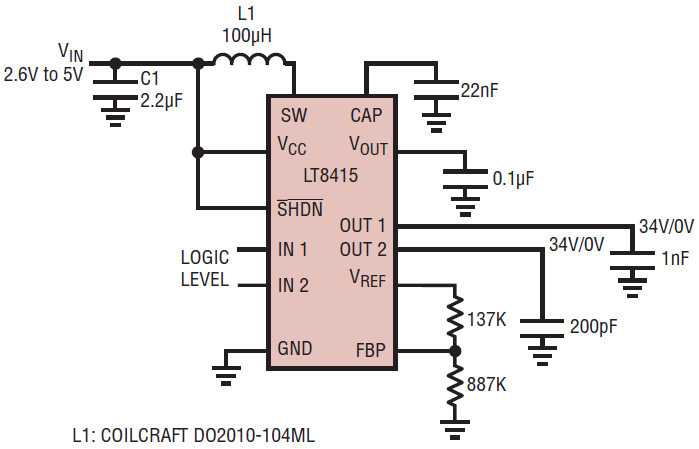
Figure 2. 2.6V–5V input to 34V dual half-bridge boost converter.
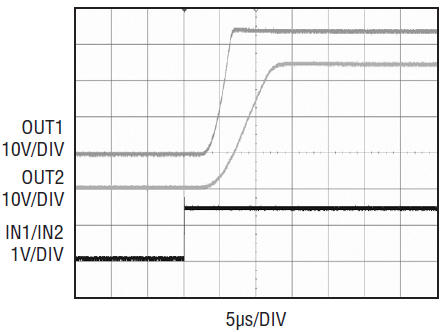
Figure 3. Turn-on delay and rise time for OUT1 and OUT2.
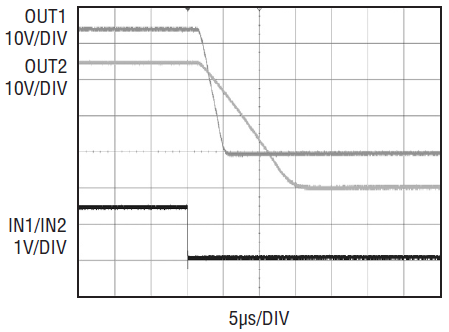
Figure 4. Turn-off delay and fall time for OUT1 and OUT2.
3V–10V Input to 16V Output MEMS Driver and Bias Supply
Figure 5 shows a 3V–10V input to 16V output converter, where the output drives the dual half-bridge and also provides bias current for other circuitry. The converter in Figure 2 can be used in a similar fashion, but the current available at the output is reduced as the output voltage is increased. See the data sheet for details about maximum output current.
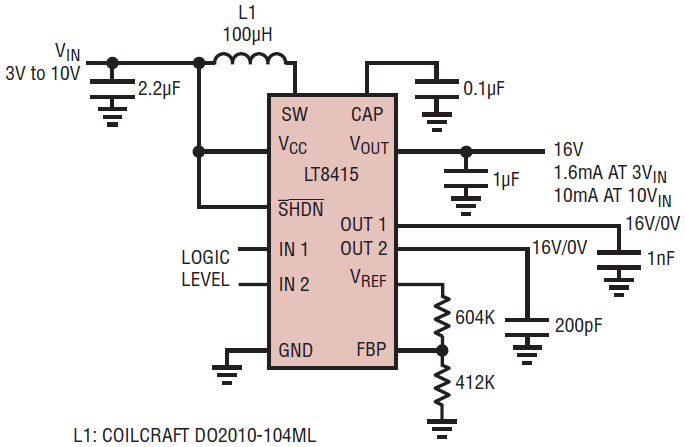
Figure 5. 3V–10V input to 16V dual half-bridge plus 16V output boost converter.
Integrated Resistor Divider
The LT8415 contains an integrated resistor divider such that if the FBP pin is at 1.235V or higher, the output is clamped at 40V. For lower output voltage levels use R1 and R2, calculating their values as instructed by the data sheet. This method of setting the output voltage ensures the voltage divider draws minimal current from the input when the part is turned off.
Conclusion
The LT8415 is an ideal match for driving low power MEMS. It integrates a step-up converter power switch and diode, a complementary dual half-bridge, and a novel switching architecture that minimizes power dissipation.
著者について
Jesus Rosalesは、アナログ・デバイセズのアプリケーション・グループ(カリフォルニア州ミルピタス)に所属するアプリケーション・エンジニアです。1995年にアソシエート・エンジニアとしてLinear Technology(現アナログ・デバイセズ)に入社し、2001年にアプリケーション・エンジニアに昇格しました。それ以来、モノリシック型の昇圧/SEPIC/反転コンバータ・ファミリと、オフライン型/絶縁型アプリケーション・コントローラを...