More Bang for Your Boost: Driving Heavier Loads with Lower Battery Voltages
More Bang for Your Boost: Driving Heavier Loads with Lower Battery Voltages
Feb 23 2022
Abstract
Bootstrapping is a technique that can be applied to most boost converters and enables the converter to run down to a lower voltage while still driving heavy loads. Many portable designs require a boost converter to convert a low battery voltage into something higher, but as the battery voltage decays, the drive to the boost converter’s FET is reduced and can sometimes reduce the current available to the output. Bootstrapping overcomes this problem and buys extra battery life while increasing the efficiency at heavy loads.
These Boosts Are Made for Workin’
The ADP1612 is a low cost, high efficiency boost converter that operates at 1.3 MHz and is ideal for consumer electronic circuits that need to be physically small. It has a shutdown pin that reduces the quiescent current to less than 2 μA and operates with an input voltage down to 1.8 V making it ideal for battery-powered electronics. However, as the battery voltage drops, its peak current falls. This can be a benefit if the battery needs to be treated gently in its last hours, but this can also lead to problems driving heavy loads with a low battery input. Bootstrapping overcomes this problem and provides high output current with high efficiency while it allows the battery voltage to run down to a much lower level.
Getting More Battery Life from a Boost Converter
Figure 1 shows the standard evaluation kit for the ADP1612. A 200 mΩ current sense resistor was added in series with the battery input to measure the input current. A large electrolytic capacitor was added to the battery input of the circuit to smooth the inductor’s current peaks so that average battery current could be measured across the sense resistor with a high degree of accuracy. The battery voltage was measured with a digital voltmeter and, hence, the input power could be calculated by multiplying battery voltage by input current. Resistive loads were added to the output and the efficiency of the converter was calculated by dividing output power by input power.
Figure 1. Evaluation kit of the ADP1612.
Probing the switch node (SW) tells us a lot about how a DC-to-DC converter is performing. When the FET is switched on, the inductor current ramps up causing the bottom of the switch node voltage to ramp, proportional to the FET’s ON resistance. The lower this voltage, the lower the ON resistance of the FET. Hence, the lower the losses in the FET for a given current. Figure 2 shows the switch node, in nonbootstrapped configuration, with a 2 V battery voltage. The bottom of the switch node voltage shows a peak value of about 180 mV.
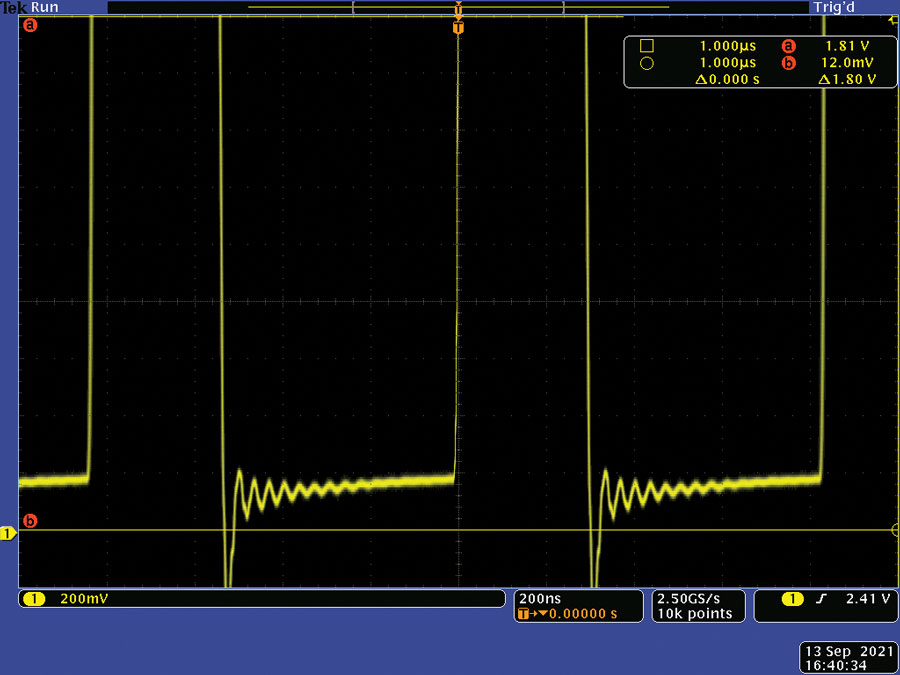
Figure 2. Switch node voltage, 2 V input, nonbootstrapped.
Increasing the battery voltage to 3 V gives the switch node waveform shown in Figure 3. Here we notice the duty cycle has gone down due to the higher battery voltage, but also that the low part of the switch node voltage is at a noticeably lower level, peaking at about 80 mV. However, since the FET current with a 3 V battery voltage is lower than that with a 2 V battery voltage, it is difficult to see if the ON resistance has indeed reduced.
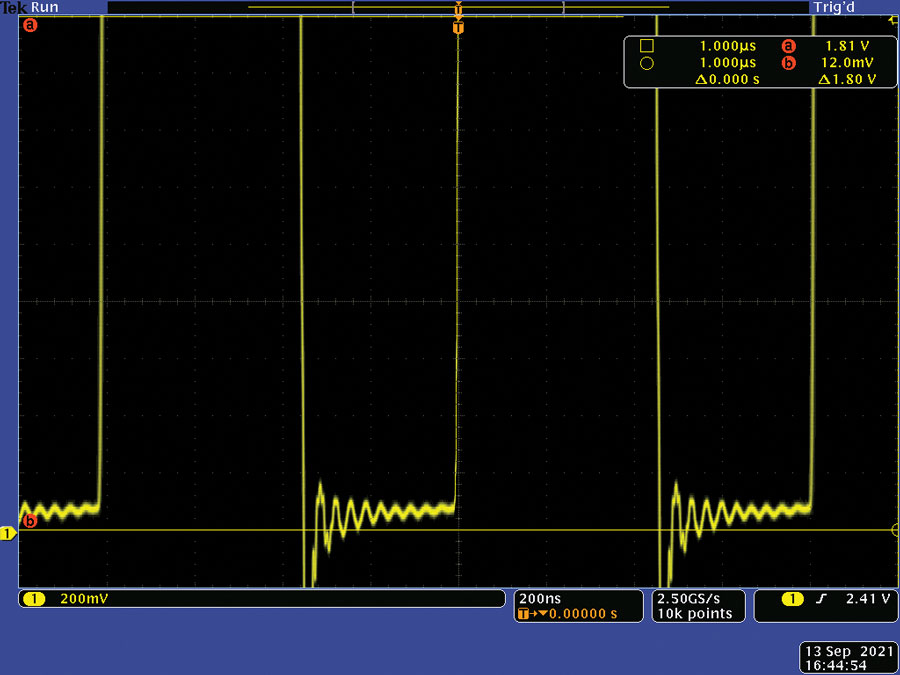
Figure 3. Switch node voltage, 3 V input, nonbootstrapped.
The circuit in Figure 1 was then converted to the bootstrapped configuration. Bootstrapping involves connecting the VIN pin of the ADP1612 to the output voltage. Once the part has started up, it is powered from the higher output voltage, therefore producing a higher drive to the FET while the ADP1612 is unaware of the battery voltage level. The modified circuit is shown in Figure 4.
Figure 4. Bootstrapping the VIN pin from the output voltage.
The Enable pin can either be connected to the battery voltage, VBATT, or the output voltage. Connecting it to the battery voltage asserts the undervoltage lockout (UVLO) if the battery voltage goes below approximately 1.7 V, while connecting it to the output voltage allows the ADP1612 to keep switching even when the battery voltage has run down to a voltage much lower than this.
Figure 5 shows the efficiency results for the nonbootstrapped and bootstrapped configurations with a battery voltage of 2 V with a measured output voltage of 4.95 V.
Figure 5. Efficiency of the ADP1612 with a 2 V input in nonbootstrapped and bootstrapped (b/s) configurations.
The efficiency curve of the bootstrapped configuration is represented by the solid line in Figure 5 and is noticeably lower at light loads. This is mainly because the quiescent current of the device (about 4 mA) now comes from the output voltage and is effectively multiplied by the factor
We can also see that the bootstrapped circuit starts to offer an efficiency improvement for heavy load currents (above about 260 mA) when operated with a low battery voltage due to the higher FET drive.
Figures 6 and 7 show the bottom of the switch node voltage in bootstrapped mode. It is important to note that bootstrapping only affects the supply voltage to the controller IC. It does not affect the power path (inductor and output diode). Therefore, we can now directly compare the 2 V bootstrapped and nonbootstrapped switch node voltages (in Figure 6 and Figure 2) and the 3 V bootstrapped and nonbootstrapped switch node voltages (in Figure 7 and Figure 3).
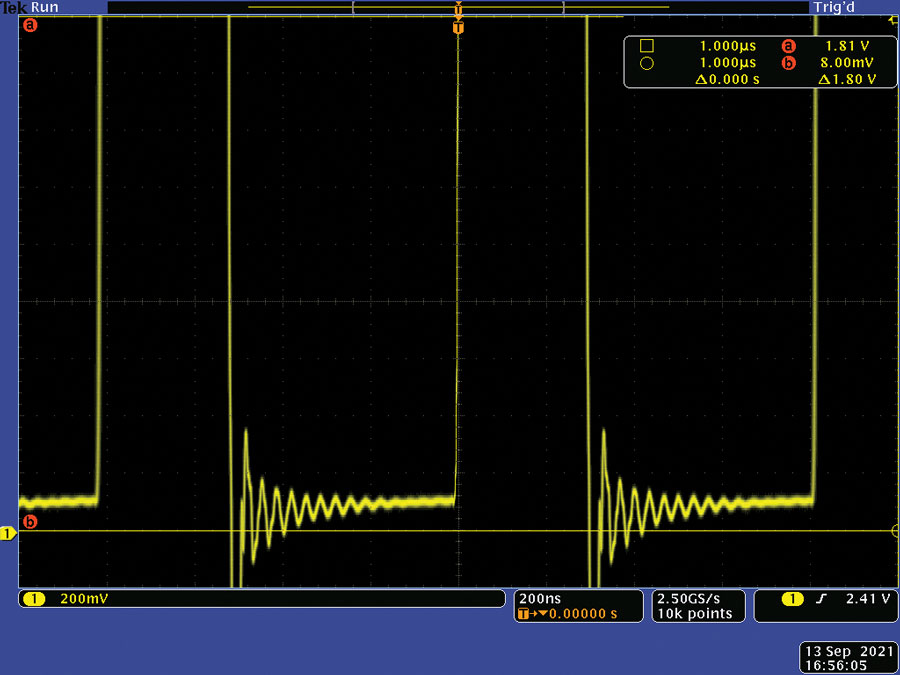
Figure 6. Switch node voltage, 2 V input, bootstrapped.
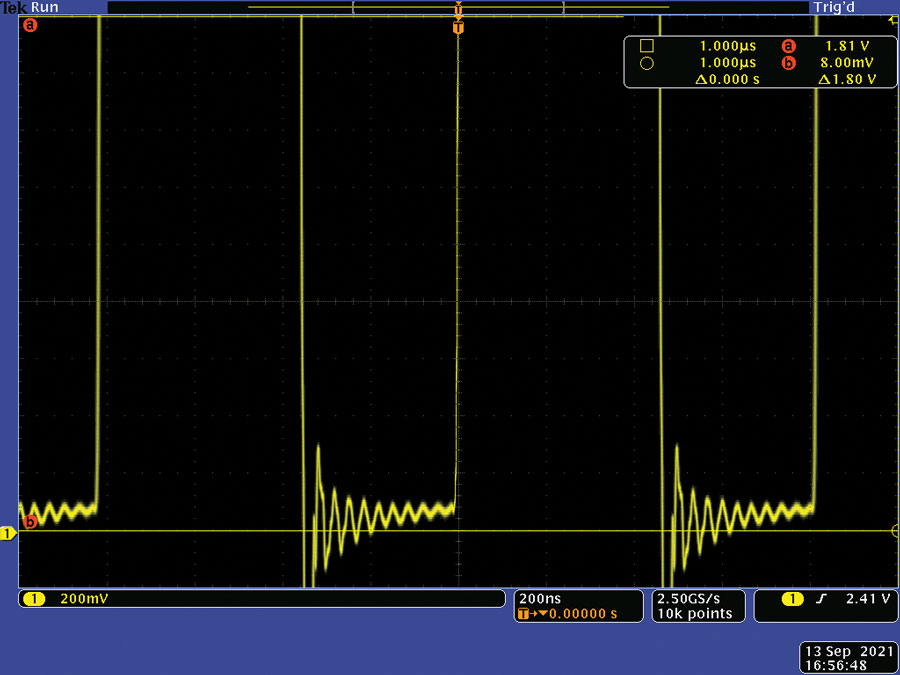
Figure 7. Switch node voltage, 3 V input, bootstrapped.
There is a clear advantage to bootstrapping with low battery voltages. With a 2 V battery voltage, the nonbootstrapped switch node voltage peaks at 180 mV compared to only 100 mV for the bootstrapped circuit, indicating a lower ON resistance FET and consequently lower losses. There appears to be little, if any, improvement in the bootstrapped circuit with a battery voltage of 3 V, with both switch node waveforms peaking at about 80 mV.
How Low Can You Go?
Another useful experiment is to see how low the battery voltage can be taken before the output voltage starts to lose regulation. Figure 8 shows the comparison between bootstrapped and nonbootstrapped modes.
Figure 8. Load current vs. minimum input voltage.
In the nonbootstrapped circuit, we see the UVLO circuit activates with battery voltages below about 1.7 V as shown by the blue curve. By contrast, the bootstrapped circuit in Figure 4 ties both the Enable and VIN pins to the output voltage (5 V), thus defeating the UVLO and therefore, allowing the circuit to run down to a much lower voltage. However, the circuit cannot create power from nowhere. The ADP1612 has a peak current limit; therefore, the higher the load current, the higher the battery voltage needs to be to furnish that load current for a fixed peak switch current. Thus, the red curve of Figure 8 increases almost linearly as load current is increased.
The minimum operating voltage is determined by the maximum duty cycle of the converter, which is about 90%. From the equation
a 5 V output and a maximum duty cycle of 90% dictate a minimum battery voltage of 0.5 V, which agrees with the results shown in the graph.
What is surprising about Figure 8 is the fact that the nonbootstrapped circuit can supply a higher load current than the bootstrapped circuit with battery voltages above 2.2 V. This is because the quiescent current of the ADP1612 is higher in bootstrapped mode as it is running from the output voltage. In addition, the ADP1612 has an efficiency less than 100%, thus further increasing the required input current to the circuit for a given load current. This results in a slightly higher required input voltage (about 150 mV) in bootstrapped mode compared with nonbootstrapped mode. As was noted earlier, the benefits of bootstrapping are not significant with higher battery voltages and the advantages that the higher gate drive brings are not enough to offset the increased losses introduced by the increased quiescent current in the bootstrapped circuit.
Other Benefits and Drawbacks
The bootstrapped configuration also has an impact on the start-up voltage of the circuit. Now the VIN pin of the ADP1612 is powered from the output, the battery voltage needs to be higher than the nonbootstrapped circuit by one Schottky diode drop. The voltage drop across a Schottky diode varies with current from about 100 mV (at a current of 50 μA) to above 200 mV at higher currents. It was found through experimentation that the start-up voltage of the nonbootstrapped circuit was about 1.75 V (equal to the UVLO threshold) while this rose to about 1.95 V for the bootstrapped circuit.
Conclusions: Are You Ready Boosts? Start Workin’
Nancy Sinatra would be proud.* Bootstrapping can be applied to any boost converter that does not disconnect the battery voltage from the output on startup. The impact of poorer light load efficiency can be mitigated by using devices with very low quiescent current. The higher start-up voltage is not often a problem since circuits are not often required to start up with a dead battery.
If the circuit has a load current that is quite light for most of its operation or a high battery voltage, then bootstrapping might not buy you any benefit. However, if the load is heavy and the circuit needs to continue operating right up to the last dying minutes of the battery, then bootstrapping is worth considering.
*These Boots Are Made for Walkin’—Nancy Sinatra, 1966
About the Authors
Simon Bramble graduated from Brunel University in London in 1991 with a degree in electrical engineering and electronics, specializing in analog electronics and power. He has spent his career in analog electronics and work...